
LEICHTFÖRDERTECHNIK
INNOVATIVE LÖSUNGEN FÜR PRODUKTION UND VERSAND
Überall dort, wo es darauf ankommt Produktionsprozesse und Versandabläufe effizient und wirtschaftlich zu gestalten, sind Komponenten und Anlagen der AMI-Leichtfördertechnik die richtige Wahl / zielführend. Mit der besonderen Fördertechnik für leichte Güter – transportiert in Behältern oder Kartons – lassen sich Intralogistikprozesse in nahezu allen Branchen, zum Beispiel im Maschinenbau, in der Automobilindustrie, in der Medizintechnik, im Pharmahandel sowie im E-Commerce und in der Papier-, Kunststoffindustrie optimieren.
Wie alle fördertechnischen Systeme und Anlagen von AMI basiert auch die Leichtfördertechnik auf einem ausgereiften Baukastensystem von Komponenten, Modulen sowie
intelligenten Steuerungssystemen und einer breiten Palette an standardisiertem Zubehör.
Mit einem auf die jeweiligen Anforderungen zugeschnittenen Leistungspaket sorgen die AMI-Experten sowohl bei Standardanlagen als auch bei individuellen Fördersystemen für eine fachgerechte, zügige und zielgenaue Projektrealsierung. Dabei reicht das Leistungsspektrum von der Beratung und Planung über die Konstruktion und Fertigung bis hin zur Montage und Inbetriebnahme. Für dauerhaft höchste Anlagenverfügbarkeit sorgt das umfangreiche AMI-Service- und Wartungsangebot an 365 Tagen im Jahr, rund um die Uhr.
AUTOMATION MATERIALFLUSS INTRALOGISTIK
ANWENDERBERICHT:
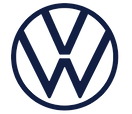
Automatisierte AMI-Förderanlage optimiert
Montageprozesse bei VW

Im Rahmen von Produktivitätsworkshops hat der Automobilkonzern VW am Standort Wolfsburg die Abläufe in den Pkw-Montagelinien auf den Prüfstand gestellt. Ein Ergebnis dieser Workshops legte den Handlungsbedarf im Anstellbereich für Heck- und Frontstoßfänger an der Montagelinie 4 der Halle 8 offen. Das bis dahin praktizierte manuelle Handling der per Routenzug angelieferten Stoßfängergestelle war nicht nur aufwendig, sondern für die Mitarbeiter auch ein Kraftakt. Abhilfe schafft nun eine elektrisch angetriebene Förderanlage der AMI Förder- und Lagertechnik GmbH, Luckenbach.
Routenzüge gehören in der Automobilproduktion zum festen Equipment in Sachen Materialflusstechnik. So auch am größten Standort der Volkswagen AG in Wolfsburg. Eingesetzt werden die Routenzüge dort u. a. zur „Just in Sequence“-Versorgung der Montagelinien mit Heck- und Frontstoßfängern. Als Ladungsträger kommen Transportgestelle aus Stahl in den Abmessungen 2,4 x 1,5 x 1,5 m (L x B x H) zum Einsatz, in denen jeweils vier Heck- und vier Frontstoßfänger Platz finden. „In der Vergangenheit mussten die Kollegen die beladenen Gestelle von den Wagen des Routenzugs an der Montagelinie in Einstellbuchten schieben“, blickt Denis Erhardt, Logistikplaner Werk Wolfsburg (PWL-P/B) der Volkswagen Aktiengesellschaft, zurück. „Eine körperlich anstrengende Tätigkeit. Vor allem, wenn man bedenkt, dass die Montage den Takt vorgibt: Alle vier Minuten benötigen die Werker an der Montagelinie ein neues Gestell.“
Das in diesem Bereich zu erschließende Optimierungspotenzial förderte ein Produktivitätsworkshop zu Tage. Erhardt: „Die in dem Workshop erarbeiteten Ergebnisse mündeten in einer signifikanten Verschlankung der Prozesse. Diese wiederum resultieren aus einer Reduzierung der Laufwege für die Werker durch den Einsatz einer Fördertechnik. Darüber hinaus lässt sich mithilfe der Fördertechnik die Übergabe der Transportgestelle ergonomisch deutlich besser durchführen.“
Effizienz auf begrenztem Raum geschaffen
Wie es bei der Integration von Anlagen der Förder- und Lagertechnik in Bestandsgebäuden mit festgelegtem Materialflusslayout im allgemeinen Usus ist, so waren auch im vorliegenden Fall der für die Fördertechnik verfügbare Raum und die verfügbare Zeit begrenzt. So haben die AMI-Techniker in der produktionsfreien Zeit zwischen den Jahren 2019 und 2020 auf einer Fläche von 14,7 mal 5,4 Meter zwei gespiegelte Förderanlagen für Heck- und Frontstoßfänger im Anstellbereich an der Montagelinie 4 in der Halle 8 aufgebaut. „Technologisches Rückgrat der Anlagen sind individuell gefertigte Komponenten auf Basis unseres Standardprogramms im Segment Schwerlastförderer“, so Sven Jesberg (Bild, rechts), Sales Manager der AMI Förder- und Lagertechnik GmbH, Luckenbach.
Die Zuführung der Gestelle in die Förderanlage übernehmen Mitarbeiter der VW-Logistik, indem sie die beladenen Gestelle vom Transportwagen manuell quer zur Laufrichtung auf einen Aufgabeförderer schieben. Um eine problemlose Übergabe sicherzustellen, wurden auf dem Hallenboden zwei Leisten aufgebracht, die für eine exakte Position der Transportwagen in Längsrichtung sorgen. Zur genauen Platzierung des jeweiligen Routenzug-Transportwagens an der Übergabestelle hat AMI darüber hinaus eine Signallichtsäule am Kopfrahmen der Fördertechnik installiert, die bei Eintreffen eines Routenzugs aktiviert wird. Jesberg: „Wir haben ferner an bestimmten Positionen der Transportwagen Reflektoren angebracht, die den vom Sensor ausgesendeten Lichtstrahl zurücksenden und so den Impuls für eine Signalleuchte auslösen. Leuchtet diese Lampe grün, weiß der Routenzugfahrer, dass der Wagen korrekt vor der Aufgabestelle platziert ist.“
Im Anschluss schiebt der Mitarbeiter – ohne großen Kraftaufwand und ergonomisch optimal – das Gestell auf den Aufgabeförderer. Die ersten Rollen der Aufgabe sind freilaufend. Über ein Mutingsystem wird der Aufgabeförderer gestartet und läuft unterstützend mit an. Wenn sich das Gestell teilweise auf dem Förderer befindet wird dieses automatisch in die Anlage transportiert. Anschließend wird das Gestell über einen zweiten angetriebenen Rollenförderer einem Eckumsetzer zugeführt. Von dort aus gelangt das Gestell (90° in Längsrichtung) über einen Schwerlastrollenförderer zum Stoßfänger-Entnahmeplatz. Weitere aufgegebene Gestelle reihen sich über die Einzelplatzsteuerung hintereinander auf. Die maximale Staukapazität beläuft sich auf vier Ladungsträger.
Am Entnahmeplatz gehen die Stoßfänger in den Aktionsbereich der Montagemitarbeiter über. Um Zugriff auf alle Stoßfänger zu erlangen, wird das Innenleben des Gestells manuell durch den Montagemitarbeiter gedreht. Aus Sicherheitsgründen ist während der Entnahme der Stoßfänger ein Automatikbetrieb nicht möglich. Der Werker fordert aktiv einen Gestellwechsel an, indem er einen Taster betätigt, und leitet somit den automatischen Fördervorgang ein. Jesberg: „Im Automatikbetrieb darf kein Mitarbeiter die Anlage betreten. Um die Voraussetzungen für die Personensicherheit zu schaffen, haben wir die Anlage an den Seiten und anteilig an den Stirnseiten mit einer Schutzeinhausung und im Bereich der Aufgabe sowie an den Entnahmestellen mit Sicherheitslichtgittern ausgestattet.“
Die leeren Gestelle gelangen über einen weiteren Eckumsetzer sowie einen Rollenförderer zum Abgabeplatz, wo das Gestell über eine Schwerlast-Gefällerollenbahn bis gegen eine manuelle Trittsperre rollt. Die Entnahme des Leerguts ist Aufgabe der Logistikmitarbeiter. Dazu wird mit dem Fuß die Trittsperre betätigt. Danach lassen sich die leeren Gestelle auf einfache Weise vom Abgabeplatz auf den Transportwagen schieben.
Im Falle einer Störung besteht die Möglichkeit, die Anlage im Notbetrieb manuell zu nutzen. Hierfür sind die Antriebe der Förderer jeweils mit einer Spannstation ausgestattet, worüber mithilfe einer Hebelmechanik der Antrieb vom Förderer entkoppelt werden kann. Zusätzlich lässt sich die Hubeinheit in den Eckumsetzer ebenfalls über einen Hebel manuell anheben und absenken. Trittbleche zwischen den Rollenförderern stellen ein problemloses Begehen der Anlage sicher. Mit all diesen technischen Features konnte AMI den Ansprüchen seitens der verantwortlichen bei VW an einen unterbrechungsfreien Betrieb der Montagelinie in vollem Umfang entsprechen.

Blick von der Entnahmeseite des Anstellbereichs für Heck- und Frontstoßfänger an der Montagelinie auf die automatische
AMI-Förderanlage
Automatikbetrieb: Auch eine Frage der Sensorik
Für den störungsfreien Automatikbetrieb der Montagelinie wird der Sensorik eine Schlüsselfunktion zuteil. So sorgen die eingesetzten Sensoren dafür, dass der Montageprozess problemlos ablaufen kann. In diesem Kontext müssen sie die Stoßfänger in den Gestellen erkennen bzw. feststellen, wann der Werker alle Stoßfänger aus dem Ladungsträger entnommen hat. „Denn nur dann darf die Anlage in den Automatikbetrieb wechseln, das leere Gestell abtransportieren und den nächsten Ladungsträger bereitstellen“, so Erhardt.
Auf diese Weise hat die Sensorik einen der wichtigen Punkte im Lastenheft erfüllt: Das automatisierte Andienen und den automatisieren Transport der Stoßfänger-Transportgestelle.
Im Einsatz ist die Anlage seit Januar 2020 und läuft seitdem störungsfrei. Erhardt: „Die mit der Investition verbundenen Ziele in puncto Reduzierung der Laufwege der Werker und des Arbeitsaufwands beim Wechseln von Stoßfängergestellen für die Logistikmitarbeiter konnten wir erreichen.“
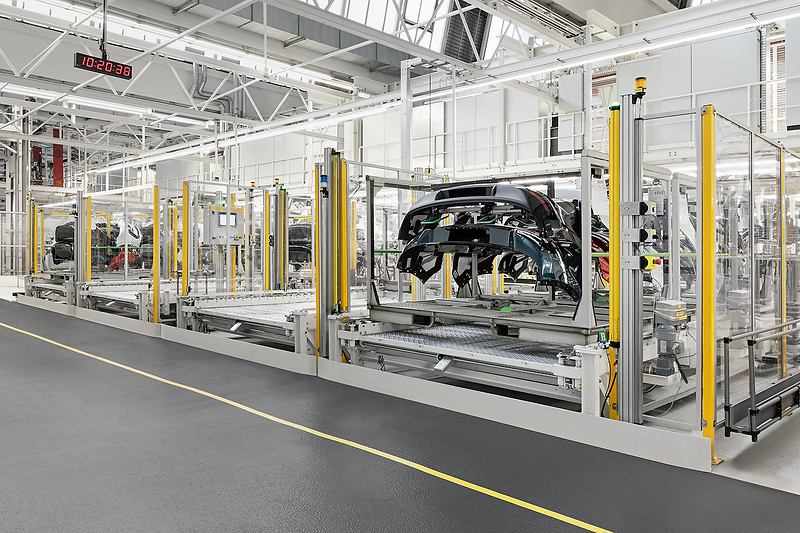
Be- und Entladestelle der Stoßfängergestelle

Der begrenzte Raum verlangte den AMI-Konstrukteuren einiges ab, um alle an die Förderanlage gestellten Anforderungen zu erfüllen
Automatikbetrieb: Auch eine Frage der Sensorik
Für den störungsfreien Automatikbetrieb der Montagelinie wird der Sensorik eine Schlüsselfunktion zuteil. So sorgen die eingesetzten Sensoren dafür, dass der Montageprozess problemlos ablaufen kann. In diesem Kontext müssen sie die Stoßfänger in den Gestellen erkennen bzw. feststellen, wann der Werker alle Stoßfänger aus dem Ladungsträger entnommen hat. „Denn nur dann darf die Anlage in den Automatikbetrieb wechseln, das leere Gestell abtransportieren und den nächsten Ladungsträger bereitstellen“, so Erhardt.
Auf diese Weise hat die Sensorik einen der wichtigen Punkte im Lastenheft erfüllt: Das automatisierte Andienen und den automatisieren Transport der Stoßfänger-Transportgestelle.
Im Einsatz ist die Anlage seit Januar 2020 und läuft seitdem störungsfrei. Erhardt: „Die mit der Investition verbundenen Ziele in puncto Reduzierung der Laufwege der Werker und des Arbeitsaufwands beim Wechseln von Stoßfängergestellen für die Logistikmitarbeiter konnten wir erreichen.“
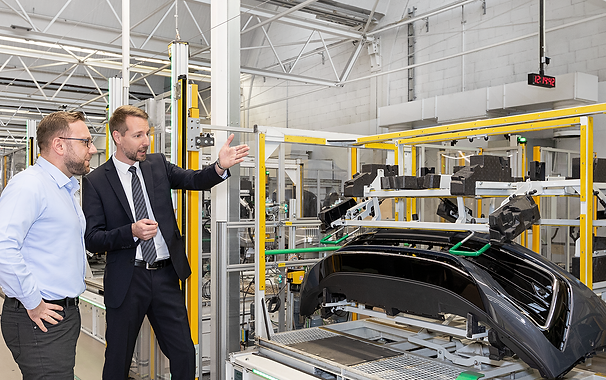
Können auf ein erfolgreiches Projekt zurückblicken: Denis Erhardt (links im Bild), Logistikplaner Werk Wolfsburg (PWL-P/B) der Volkswagen Aktiengesellschaft, und Sven Jesberg, Sales Manager der AMI Förder- und Lagertechnik GmbH, Luckenbach