
LEICHTFÖRDERTECHNIK
INNOVATIVE LÖSUNGEN FÜR PRODUKTION UND VERSAND
Überall dort, wo es darauf ankommt Produktionsprozesse und Versandabläufe effizient und wirtschaftlich zu gestalten, sind Komponenten und Anlagen der AMI-Leichtfördertechnik die richtige Wahl / zielführend. Mit der besonderen Fördertechnik für leichte Güter – transportiert in Behältern oder Kartons – lassen sich Intralogistikprozesse in nahezu allen Branchen, zum Beispiel im Maschinenbau, in der Automobilindustrie, in der Medizintechnik, im Pharmahandel sowie im E-Commerce und in der Papier-, Kunststoffindustrie optimieren.
Wie alle fördertechnischen Systeme und Anlagen von AMI basiert auch die Leichtfördertechnik auf einem ausgereiften Baukastensystem von Komponenten, Modulen sowie
intelligenten Steuerungssystemen und einer breiten Palette an standardisiertem Zubehör.
Mit einem auf die jeweiligen Anforderungen zugeschnittenen Leistungspaket sorgen die AMI-Experten sowohl bei Standardanlagen als auch bei individuellen Fördersystemen für eine fachgerechte, zügige und zielgenaue Projektrealsierung. Dabei reicht das Leistungsspektrum von der Beratung und Planung über die Konstruktion und Fertigung bis hin zur Montage und Inbetriebnahme. Für dauerhaft höchste Anlagenverfügbarkeit sorgt das umfangreiche AMI-Service- und Wartungsangebot an 365 Tagen im Jahr, rund um die Uhr.
AUTOMATION MATERIALFLUSS INTRALOGISTIK

Wenn es um die Qualität ihres umfangreichen Fleischwarensortiments geht, haben bei der Hülshorst Feinkost GmbH, Harsewinkel allerhöchste Standards – auch in puncto Nachhaltigkeit, – das sagen. Unterstützt wird die im Rahmen umfangreicher Baumaßnahmen neu gestaltete Produktion dabei von einer vollautomatisierten Endverpackungslinie der AMI Förder- und Lagertechnik GmbH, die die Anforderungen an die Nachhaltigkeit erfüllt und höchste Anlageneffizienz bietet.
Als es bei der Hülshorst Feinkost GmbH darum ging einen stärkeren Fokus auf die Automatisierung und Nachhaltigkeit zu legen, war dies mit umfangreichen Bau- und Umbaumaßnehmen sowie der Konzentration von zwei Standorten auf nur noch den in Harsewinkel verbunden und zugleich das größte Investitionsvorhaben der Unternehmensgeschichte. Im Jahre 1989 von Hubert Hülshorst zunächst als Zerlegebetrieb für Schweinefleisch gegründet, so produziert man heute Fleischconvenience-Produkte in einer großen Vielfalt. Ob zum Beispiel Frikadellen, Schnitzel, Burger, Pfannengyros, Gyrosspieße, Cevapcici, Hackfleisch, Braten, Rouladen, da ist für jeden Geschmack etwas dabei. „Unsere Kunden“, so Christoph Hülshorst (Bild 1, links), Geschäftsführer der Hülshorst Feinkost GmbH, „das sind unter anderem Großverbraucher, die Systemgastronomie oder der Snack-Bereich, wissen unser breites Angebot traditioneller, heimischer Küche und internationaler Spezialitäten und deren Qualität zu schätzen“.
Da dieses stetig wachsende Angebot, in Verbindung mit steigenden Kundenwünschen, auch Anforderungen an eine effiziente und nachhaltige Produktion stellt, entschloss sich das Geschäftsführerteam, Christoph und Philipp Hülshorst zur Durchführung umfassender Bau- und Modernisierungsmaßnahmen. Dahinter stand, neben der Konzentration auf nur noch den Standort in Harsewinkel, die Vorgabe sowohl beim Neubau als auch bei der Modernisierung und Neukonzeption der Produktion einen noch stärkeren Akzent auf die Nachhaltigkeit und Automatisierung zu setzen. Im Ergebnis bedingten diese Maßnahmen den Bau eines neuen Gebäudekomplexes inklusive neuer Produktionslinien für das gesamte Hülshorst Sortiment und deren Anbindung an eine ebenfalls neue Endverpackung sowie einer Schwerlastförderanlage für den Transport versandfertiger Paletten ins neue Tiefkühllager.
Mit gelebter Partnerschaft zum Ziel
Auf der Suche nach einem geeigneten Partner zur Realisierung der automatisierten Endverpackungslinie wurde Hülshorst auf die AMI Förder- und Lagertechnik GmbH aufmerksam und nahm Kontakt zu dem Intralogistikspezialisten auf. Bereits in den ersten Gesprächen zeigte sich die Hülshorst Geschäftsführung von der partnerschaftlichen, schnellen und fachlich überzeugenden Herangehensweise an die formulierte Vorstellung überzeugt. „Auf die ersten Planungen“, resümiert Sven Jesberg, Sales Manager bei der AMI Förder- und Lagertechnik GmbH, „folgte dann die Auftragsvergabe an uns.“
Das war dann zugleich auch der Startschuss für die finale Planung, Projektierung und Realisierung einer voll automatisierten Endverpackungslinie mit vorgeschalteten Kartonverschließern, anschließender Etikettierung und zugehöriger Fördertechnik, auch für den Transport ins angebundene Tiefkühllager.
Hinter dem Bau- und Modernisierungsprojekt stand – über alles betrachtet – der Anspruch im unternehmerischen Handeln noch umweltbewusster, ressourcenschonender und nachhaltiger agieren zu können. So kam im neuen Gebäude, gebaut nach KFW 55 Standard, zum Beispiel durchgehend modernste energieeffiziente Technik zum Einsatz und beträgt der Primärenergieverbrauch sowie der CO₂-Emissionswert nur 55 Prozent der gesetzlichen Forderung.

Per Etagenförderer gelangen die Gebinde von der Ebene der Produktionslinie 1 ins Erdgeschoss
Gute Planung ist die Basis
Nachhaltigkeit und Effizienz standen auch im Mittelpunkt als es um die Planung und Realisierung von Produktion, Materialfluss und Endverpackung ging. „Da unsere Prozesse bisher weitgehend manuell abliefen, war es für uns erklärtes Ziel, verstärkt auf automatisierte Abläufe zu setzen“, erläutert Christoph Hülshorst.
Das gilt sowohl für die Produktion und die zugehörigen vier neuen Linien für die jeweiligen Fleischconvenience-Artikel als auch für den Bereich der Endverpackung und die Fördertechnik für den Transport ins neue Tiefkühllager.
In diesem Kontext wird der vollautomatisierten Endverpackung eine wesentliche Bedeutung für die Gesamteffizienz der Intralogistik zu Teil. Hier werden die von den jeweiligen Produktionslinien auflaufenden und mit Produkten aus dem Sortiment von Hülshorst gefüllten Kartons verschlossen, etikettiert, von zwei 5-Achs-Robotern palettiert. Anschließend wird die Palette gestretcht und per Schwerlastfördertechnik ins neue Tiefkühllager transportiert. Um dieses Portfolio, zumeist gegarte Fleischconvenience-Artikel, vom Schnitzel über Frikadellen bis zum Gyros-Spezialtäten sowohl in puncto höchster Qualität, einen effizienten Materialfluss als auch in Bezug auf die Nachhaltigkeit herstellen zu können, wird schnell deutlich, dass dem Wirkungskreis Produktion, Intralogistik und Verpackung eine Schlüsselfunktion zu Teil wird.
Übergabepunkt von der Produktion also von den vier Produktionslinien zum automatischen Endverpackungsbereich sind die Kartonverschließer von denen an jeder Linie einer installiert ist. Am Übergabepunkt werden die mit den Fleischconvienence-Produkten von Hülshorst befüllten Kartons von den Kartonverschließern an der Ober- und Unterseite verschlossen. Danach läuft der jeweilige Karton über einen Schrägrollenförderer, wo er an einer Referenzkante ausgerichtet und im Anschluß im Durchlauf von der Seite automatisch etikettiert wird.
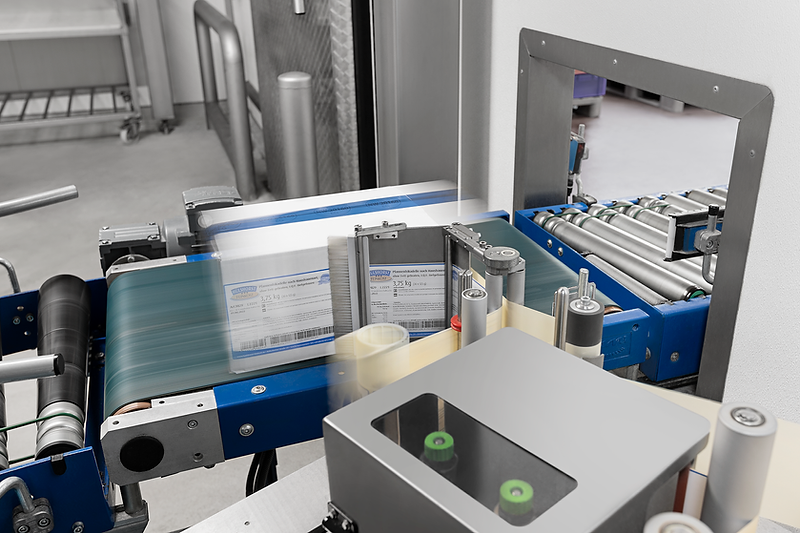
Letzte Station vor der Roboterpalettierung. Ein fertig gepackter Karton wird im Durchlauf automatisch etikettiert
Automatisierte Endverpackung schließt Effizienzkreis
Die Anbindung der Produktionslinien an die automatisierte Endverpackung und die damit verbundenen Teilprozesse wurde von den AMI-Experten so konzipiert, dass eine höchst mögliche Auslastung und Systemeffizienz sichergestellt ist. Für den Materialfluss ergibt sich damit ein konsequenter Ablauf. So werden Artikel der Produktionslinien 2 (Frikadellen), 3 und 4 (z.B. Gyros) vom Erdgeschoss über Lifte ins Obergeschoss befördert, wo die Produktlinie 1 (Schnitzel) angeordnet ist. Über diese vier Linien gelangen die mit den jeweiligen Convienenceartikeln gefüllten Kartons über eine Hauptstrecke flurfrei in den automatisierten Endverpackungsbereich und damit zu den beiden 5-Achs-Robotern. Zuvor werden die Leerpaletten entstapelt und den Robotern automatisch zugeführt.
Vor dem Eintreffen an den Robotern werden die Kartons gescannt und von der Steuerung entschieden, welcher Karton von welchem Roboter palettiert wird. Dafür werden die Kartons per Riemenhubumsetzes sortenrein auf vier Stiche (zwei je Roboter) ausgeschleust. Die Kartons werden immer zu zweit an einer Referenzkante ausgerichtet. Der Roboter greift zwei Kartons gleichzeitig und setzt diese dem Lagebild entsprechend auf der Palette ab. Nach einer Lagenbildung werden Zwischenlagen durch den Roboter aufgelegt. Pro Stunde werden 1083 Gebinde palettiert.
Nach dem Palettieren und Strechten werden die versandfertigen Paletten über Kettenumsetzer auf die Schwerlaststrecke übergeben und gelangen darüber ins Tiefkühhlager, von wo aus sie dann auf den Weg zu den Kunden gebracht werden

Hier läuft alles vollautomatisiert. Roboterpalettierung mit anschließendem Stretchautomat (rechts)
Fazit
Bringt man das Neu-und Umbauprojekt bei Feinkost Hülshorst auf den Punkt, so steht fest, dass die gesteckten Ziele in puncto Nachhaltigkeit und Automatisierung in vollem Umfang erreicht wurden. Wichtigen Anteil daran hat die automatisierte Endverpackungslinie, die für eine systematische Palettierung per Roboter sorgt und damit die Gesamteffizienz im Wirkungskreis von Produktion und Intralogistik maßgeblich unterstützt.

Geschäftsführer Christoph Hülshorst (links) und AMI Manager Sven Jesberg stimmen die Feinplanung der automatisierten Endverpackungslinie ab