
LIGHT CONVEYOR TECHNOLOGY
INNOVATIVE SOLUTIONS FOR PRODUCTION AND SHIPPING
Wherever it is important to make production and shipping processes efficient and economical, components and systems from AMI light conveyor technology are the right choice / expedient. With the special conveyor technology for light goods - transported in containers or boxes - intralogistics processes can be optimized in almost all sectors, for example in mechanical engineering, in the automotive industry, in medical technology, in pharmaceutical trade as well as in e-commerce and in the paper and plastics industry .
Like all conveyor systems and plants from AMI, the light conveyor technology is also based on a sophisticated modular system of components, modules and
intelligent control systems and a wide range of standardized accessories.
With a service package tailored to the respective requirements, the AMI experts ensure professional, rapid and targeted project implementation for both standard systems and individual conveyor systems. The range of services extends from consulting and planning through design and manufacture to assembly and commissioning. The comprehensive AMI service and maintenance offer ensures the highest level of system availability, 365 days a year, around the clock.
AUTOMATION MATERIALFLUSS INTRALOGISTIK
USER REPORT:
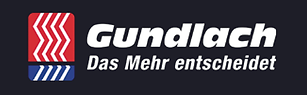
Living partnership
Reifen Gundlach and AMI realize "wheel sorter"

The company headquarters of Reifen Gundlach and AMI Förder- und Lagertechnik are only around 30 kilometers apart as the crow flies. However, it is not only due to their close proximity that the two companies have enjoyed a good working relationship for years. The realized systems also deliver what the conveyor technology manufacturer promised. One example of the partnership in action is the implementation of a shipping sorter system at Reifen Gundlach GmbH's logistics center in Daufenbach.
From a single fitting workshop, the company Reifen Gundlach, headquartered in Raubach, has developed over more than 45 years into a major player in the wholesale of tires and wheels and a supplier of complete wheels. The large number of brands from which customers of the company, which today employs more than 390 people, can choose is testimony to this. The catalogs include the products of all leading manufacturers and, in the aluminium wheel segment, the company's own brands OXXO, Advanti Racing, Enkei Tuning and MAK Wheels. A feel for the needs of customers, which include specialist tire dealers and wholesalers as well as car manufacturers and importers, has always been one of the key guarantees of success.
However, the focus on internal processes has also always played an important role in strategic considerations. In 2008, for example, the most modern complete wheel assembly line in Europe was put into operation at the Daufenbach logistics center. Reifen Gundlach thus equipped itself for the challenges of the changing market and established itself as a system provider. In this assembly line, which consists of several stations, the components tires and rims become one unit. These units, known as complete wheels in technical jargon, are balanced and measured in the assembly line and then assembled into shipping units. A shipping unit consists of a maximum of two tires. "This is mainly due to the weight of the shipping units," says Alexander Mauer (image 1, right), Technical Manager at Reifen Gundlach GmbH, getting to the heart of the matter. "Another aspect is also important for physical shipping and therefore for our logistics partners. We promise our customers that they will receive their wheels within 24 hours of receiving their order. Shipping takes place throughout Europe."
But back to internal logistics. Cardboard boxes are used to protect the rims from scratches or other damage on the way to the customer. The shipping units formed by the robots then pass through a shrink tunnel. There, the shipping unit is wrapped in shrink film, giving it the stability it needs to reach the recipient undamaged. With a shipping label attached, the unit is ready for transfer to the shipping area.
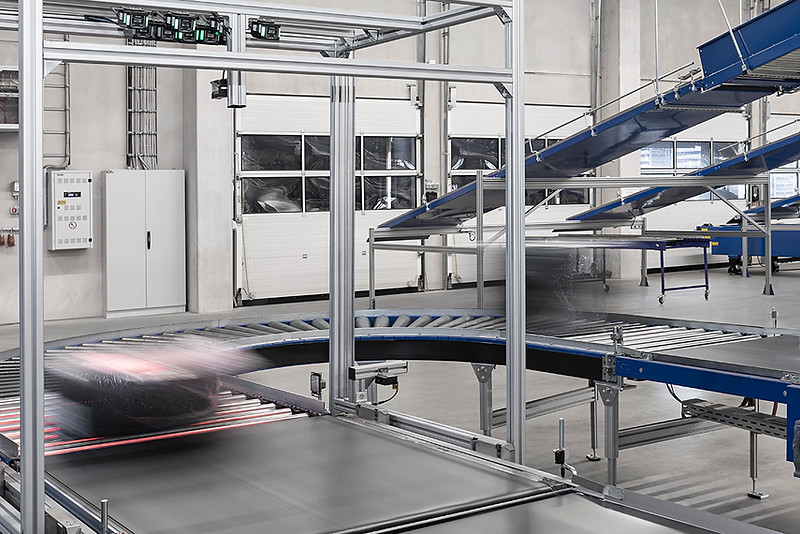
Link between order picking and shipping
The final station in the production process is the dispatch zone. Here, the conveyor system from AMI, which in this case serves as a sorter for the provision of the shipping units at one of the twelve loading gates, is the efficient link between the picking area and shipping.
"We also implemented the existing conveyor technology in the order picking area with AMI more than ten years ago," says Mauer. "And as we have had good experiences with the system and the support from the AMI team over the years, our 'neighbor' from Luckenbach was our first point of contact for the current sorter project. However, we also wanted to give other suppliers the chance to prove themselves."
But the technical concept developed by AMI, including the conveyor components such as the rotary feeders, which sort the shipping unit consisting of two compact tires at the appropriate point to one of the twelve end points for shipping, convinced Mauer. Mario Weber (image 1, left), Sales Manager at AMI Förder- und Lagertechnik GmbH: "The rotary feeders are an integral part of our broad product and system portfolio and are ideally suited to efficiently designing sorting and distribution processes." Adapted to the conveyed goods of cardboard boxes and shrink-wrapped tire stacks, the rotary feeders create the conditions for a stable process and a system output of 1,800 shipping units per hour.
As soon as the AMI rotary discharge unit receives an electrical impulse, the arm is rotated by 180°. The pusher plate ejects the conveyed goods, in this case the complete wheels, from the row (Fig. 2). Thanks to a special gearbox, it remains parallel to the piece goods at all times in order to discharge them precisely and without errors. The integration of an additional stroke also enables gentle ejection from closed rows of conveyed goods.

AMI three-house feeder

The process in detail
The overall concept of the conveyor technology consists of the merging of three conveyor lines, which serve a total of twelve end points for dispatch via a "sorter". The majority of the conveyor technology runs at a height of approx. 3,300 mm. Mauer: "Hall space is also a rare commodity for us. With this in mind, it was important to us that most of the conveyor technology is elevated in order to free up space for other tasks."
The units coming from picking are brought together in a controlled manner on a centering conveyor. The shipping units then pass a scanner bridge, where the information stored in the barcode label is recorded and transferred to the ERP material flow control system. The software uses this information to determine which of the twelve destinations the goods are destined for. After being brought together on a conveyor line and passing through the scanner station, the shipping units are transported from a working height of 800 mm to a conveyor height of 3,300 mm via a continuous conveyor line. "Before they are sent to the individual discharge points," says Alexander Völz, project manager at AMI, "the parcels or stacks are separated once again to ensure that the distances between the shipping units are even." The goods are discharged at the various destinations and then loaded onto trucks by employees. "If goods cannot be allocated to an end point, the parcels or stacks are fed back into the cycle at the end of the lane. This ensures that they are reallocated to the discharge point."
Continuous conveyor line with a conveying height of 3,300 mm

Goods exchange key
Continuation of the cooperation
As previously mentioned, Reifen Gundlach and AMI can look back on many years of cooperation. "As a medium-sized provider of automated intralogistics solutions," says AMI Managing Director Stefan Brenner, "we attach great importance to a partnership-based relationship with our customers. As with the shipping sorter project, we bring together the logistical objectives of our customers with the potential of our technical solutions and ultimately lead the project to success".
And this partnership is set to continue, because: The need for modernization in the order picking area is becoming apparent. Discussions about replacing the system are already well advanced - true to the maxim: "Never change a winning team."